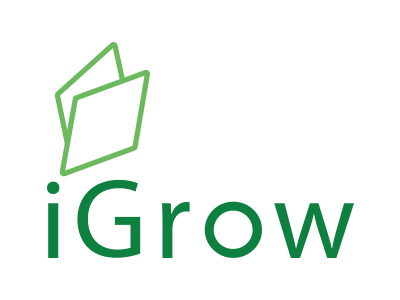
Welcome to iGrow News, Your Source for the World of Indoor Vertical Farming
EAT LOCAL + HEALTHIER + GREENER + FRESHER
As Americans increasingly reject cheap, processed food and embrace high-quality, responsibly-sourced nutrition, hyper-local farming is having a moment
EAT LOCAL
EAT FRESHER
EAT HEALTHIER
EAT GREENER
Photo: AeroFarms
image taken by photographer Holly Challinor, Jones Food Company Ltd.
HELIPONIX
TOP USAGE OF FARMLAND BY STATE
ALL OF THE AG LAND IN THE WORLD
AmplifiedAg Inc. Completes $40MM In Capital Raise, Expanding Global Technologies And Vertical Roots Indoor Farms Across The Southeast
AmplifiedAg Inc.™, fast-growing agtech industry leader on a mission to provide global access to safe food, announced today that the company has completed $40 million in equity financing.
August 9, 2021
CHARLESTON, S.C., /PRNewswire/ -- AmplifiedAg Inc.™, fast-growing agtech industry leader on a mission to provide global access to safe food, announced today that the company has completed $40 million in equity financing. The funding will support the continued expansion of the company's world-leading hydroponic container farm, Vertical Roots and further development of the company's holistic operating system, AmpEDGE™, which uniquely combines environment monitoring and controls with business operations for end-to-end indoor farm management.
"Our demonstrated ability to scale our indoor farms and technology is leading to discussions with strategic and financial partners, and we expect to consummate additional financing later this year to further accelerate Vertical Roots' presence across the Country," said Don Taylor, CEO of AmplifiedAg.
Vertical Roots' rapid success exemplifies the time, profitability, operational growth efficiency, and superior product quality AmplifiedAg farms and technology achieve. In less than four years, Vertical Roots has grown to be the largest hydroponic container farm in the world growing multiple varieties of mature, fresh leafy greens. The company currently operates three farm sites in Charleston, S.C., Columbia, S.C., and Atlanta, Ga. with produce available at 1,700 major grocery stores across 12 states including retailers such as Publix, Harris Teeter and Whole Foods, as well as schools, universities, and restaurants.
The current round of funding will support the installation of farms in north and central Florida, extending Vertical Roots' dominant position as the leading CEA and vertical farming business in the southeast market.
AmplifiedAg implements a distinctive strategy to operate Vertical Roots farms directly at distribution facilities, eliminating a massive leg of produce transportation in order to reduce emissions and provide communities with fresh, locally grown produce. Vertical Roots current focus is on nutritious, mature lettuce varieties that are celebrated for their flavor, freshness and being 100% pesticide-free.
Taylor added, "We're dually focused to deploy Vertical Roots farms across the country as close to the point of consumption as possible, while advancing and expanding AmplifiedAg's global network of proven technologies and farms to others in the CEA industry."
About AmplifiedAg, Inc.
AmplifiedAg, Inc.™ is an agtech industry visionary on a mission to provide global access to safe food. The company manufactures indoor vertical container farms, hydroponic systems, and disruptive seed-to-sale SaaS-based technologies. AmplifiedAg provides holistic indoor farming solutions to sustainably grow and distribute food anywhere in the world.
AmplifiedAg owns and operates Vertical Roots, the largest hydroponic container farm in the World with produce in over 1,700 grocery stores nationwide. Learn more at www.amplifiedaginc.com. Growing Food for a Growing World.
The Farmory: Is Indoor Fish Farming A Viable Way of Tackling Declining Fish Populations?
The Farmory, an urban farming nonprofit, is the only indoor fish hatchery in Wisconsin. The nonprofit focuses on sustainable growing practices for both greens and gills
By John McCracken
August 6, 2021
For decades, Green Bay Wisconsin National Guardsmen stored munitions and trained new recruits in a stucco-clad, Chicago Street building built in 1918.
Now, the building is home to hundreds of fish babies.
The Farmory, an urban farming nonprofit, is the only indoor fish hatchery in Wisconsin. The nonprofit focuses on sustainable growing practices for both greens and gills. When it was founded in 2016, the focus was on growing produce indoors using aquaponic systems to both teach and provide a new source of food in the state’s harsh winters. As the program grew, they introduced percids such as yellow perch, walleye and sauger into their arsenal.
Executive director Claire Thompson said most aquaponic operations use tilapia because of its cheap price point due to massive global exports.
“There’s also some perceptions about (tilapia) here, especially in the Midwest, that it’s not as good of a fish,” said Thompson.
The Farmory settled on growing yellow perch to complement their vegetable production because of its beloved place on Wisconsin plates and its volatile population over the years.
They soon discovered a problem. No one was growing perch indoors yet.
“That led us down the road toward ‘more research needs to be done,’” said Thompson. “We need to be able to set up our own hatchery to produce a steady and consistent supply of year-round, feed-trained fingerlings that are grown from the egg in an indoor environment.”
In the bottom level of The Farmory, budding fish are separated by a bio-secure room and health protocols. Volunteers and entrepreneurial and technician students take turns monitoring temperatures in the complex hatchery. Each separate tank mirrors life cycles and seasons of growing yellow perch and their walleye cousins. During a late June visit, an insulated tank is sealed shut and a quick peak inside shows adolescent perch huddled together for warmth. The fish don’t know about the humid Midwest summer outside because their faux-winter hovers around a chilly 30 degrees Fahrenheit.
The Farmory (Photo Credit: John McCracken for Great Lakes Now)
Schools in session
Being a nonprofit allows The Farmory to not have to worry about mass production or profit margins as much as for-profit hatcheries that already exist on slim margins. Instead, they worry about being a stepping-stone for future fish farmers.
The Farmory offers 12-week technical programs that provide hands-on trainings and lectures from researchers and ichthyologists. Since The Farmory launched both pathway programs in 2020, they have had 34 graduating students.
Thompson said that for students interested in aquaculture there are only two options in the state. Students can go to a four-year program at either University of Wisconsin-Stevens Point or UW-Milwaukee.
For the students coming through The Farmory’s doors—who range from recent high school graduates to retirees—fish-wrangling fares better than test-taking in the growing industry.
“There’s a lot of jobs in the aquaculture industry that don’t require a four-year degree,” Thompson said. “You have to have people with basic technical skills.”
The Farmory’s students are much like their customers. Their interest and aspiration range from basement or backyard hobby farming to scalable commercial production. The Farmory grows fingerling perch until they are between 2 to 4 inches and then customers take them to grow them to adult size for spawning or frying.
In 2020, they had 60 customers and sold fish across state lines to Michigan, Ohio and Minnesota. Thompson said most customers bought between 100 and 500 fish, but a handful purchased thousands of perch pounds to fuel their own commercial fishery endeavors.
“We want to be able to secure a local food supply. We also want to teach people about aquaculture as a viable business opportunity,” said Thompson.
The Farmory (Photo Credit: John McCracken for Great Lakes Now)
Problems come with being new
Being the only indoor perch hatchery comes with its challenges though.
The COVID-19 pandemic hindered The Farmory’s first hatching year. They weren’t able to get brood stock up to full capacity due to supply-chain complications. The urban farm is working on getting their population to a sustainable level.
Additionally, Thompson said that there is a lack of research and applied standards when it comes to growing perch indoors.
“It’s not like any other agricultural commodity product like dairy or chickens,” said Thompson.
Thompson said yellow perch have an innate biology barrier, where survival is harder to come by—something that is important for an organization focused on producing and spreading young perch. Perch also don’t have a set diet. As of now, The Farmory feeds their perch a trout diet, which Thompson said is slightly fattier.
“We have to find a way to get enough people into the business of (indoor fisheries) to we can work with feed companies to be able to develop affordable feed,” said Thompson.
On the other end of the process chain, Thompson said a decline in the perch population since the booming years of yore has led to a lack of skilled fish processers and sustainable operations.
“Because of the decline of Great Lakes commercial fishing, we’ve also seen a decline in processors to clean and process fish,” said Thompson.
Smaller, sustainable scale
Sharon Moen echoed a lot of Thompson’s observations of the industry at large.
Moen is an outreach specialist with Wisconsin Sea Grant— a statewide research and stewardship program dedicated to the resources of Great Lakes—in charge of the Eat Wisconsin Fish Initiative. Eat Wisconsin Fish was established in 2013 to become a hub for information and resources for the state’s fish producers and consumers.
Moen said the many people in the industry believe the future of fish farming is heading indoors because of the effects of climate change on the industry, its habitats and the fish themselves.
“Algae blooms and invasive species can’t get into the water,” Moen said of indoor, contained aquaculture systems.
Moen also said that the way consumers and producers import and export massive numbers of commodities has a continued effect on the planet due to gas emission.
“We have to stop carting things around the globe in order to really truly cut down on carbon emissions,” said Moen. “We need to learn to eat and grow our food more locally.”
In the past year, Moen observed how breaks in the supply chain—caused by global catastrophe such as the COVID-19 pandemic—make everyone and every supplier vulnerable. Just as the majority of The Farmory’s students are scaling down, many suppliers are focused on local, small-scale consumption.
“I think most (fisheries) are very modest people raising for their local community consumption,” said Moen.
Moen said to alleviate stress on perch’s floundering population and high price point – which she observed at upwards of $20 a pound last year – consumers could switch to a more abundant species like whitefish.
Both Moen and Thompson pointed out that adjusting to problems in the industry, whether you’re growing fish in a bedroom tank or in cavernous outdoor ponds, takes agility and a love for fish.
“It’s like gardening,” Moen said. “You have to have a knack for it and take care of what you’re growing.”
European Pension Managers Go Big For Indoor Ag as Equilibrium Closes $1.1bn CEA Fund
Equilibrium Capital, a US-based private sustainable finance and ESG funds manager, has closed its second indoor ag fund on just over $1 billion – well beyond its $500 million target.
By Louisa Burwood-Taylor
July 8, 2021
Equilibrium Capital, a US-based private sustainable finance and ESG funds manager, has closed its second indoor ag fund on just over $1 billion – well beyond its $500 million target.
Controlled Environment Foods Fund II (CEFF II) raised $1.02 billion from a group of institutional investors, mostly pension funds, with a strong showing from Europe, according to Equilibrium CEO Dave Chen. Sweden’s AP4 was one of five anchor investors that took over half of the total fund alongside two large UK pension managers, he added.
CEFF II will invest in high-tech greenhouses, indoor, vertical farms, and other sectors that need controlled environment agriculture (CEA) facilities such as alternative proteins and aquaculture.
“The strong investor demand reflects a drive to real assets” and sustainability by large institutional investors, combined with an “interest in agriculture and food systems,” Chen told AFN.
“There is a sense that ag is going through several simultaneous disruptions and that creates an opportunity.”
A press release announcing the fund closing states that investors and retailers “are increasingly looking for more sustainable, and less volatile, ways to invest in and scale agriculture.
“CEA shifts agriculture from a land-centered industry where the land, geography, and weather determines what can grow, into a climate-resilient industry that can now focus on the consumer’s demand for the fresh, safe, and regional fruits and vegetables they want to eat,” it continues.
For Portland, Oregon-based Equilibrium — which has funds across environmental and sustainability verticals including ‘green’ real estate, water, wastewater, and outdoor agricultural production — CEA is a compelling investment opportunity for its ability to dramatically increase the productivity of food production “per unit of resource input [and] land use,” said Chen.
“The ability to ride a tech innovation curve, locate farms regionally for quality and resilience, adapt to climate change, and capture demand from retailers and food service” also make it attractive, he added.
Asked where he expects the market share for CEA-produced food to be in five years, he estimated upwards of 30-50%. “Tomatoes are already there,” he said.
Equilibrium is predominantly a real assets investor, owning or investing in indoor farming facilities and greenhouses, but it also buys equity stakes in operating companies. CEFF II will invest between $10 million and $125 million per deal, primarily across North America. It has made three investments to date — two in the US and one in Mexico — mostly in mature high-wire crops like tomatoes, peppers, and cucumbers, as well as the emerging categories of leafy greens and berries.
Equilibrium’s $336 million Fund I portfolio includes indoor ag companies such as AppHarvest — which went public earlier this year via a SPAC merger — Revol Greens, and Little Leaf Farms.
AppHarvest Names Julie Nelson EVP, Operations to Build Industry-Leading Manufacturing and Supply Chain Capabilities and Drive Performance Across Network of Farms
AppHarvest to leverage Nelson’s proven experience at PepsiCo, McKinsey to drive productivity across the company’s network of high-tech indoor farms and optimize operations to support profitable growth
August 5, 2021
AppHarvest to leverage Nelson’s proven experience at PepsiCo, McKinsey to drive productivity across the company’s network of high-tech indoor farms and optimize operations to support profitable growth
MOREHEAD, Ky., Aug. 05, 2021 (GLOBE NEWSWIRE) -- AgTech leader AppHarvest (NASDAQ: APPH, APPHW), a public benefit company and certified B Corporation focused on farming more sustainably using up to 90% less water than open-field agriculture and only recycled rainwater, has named Julie Nelson its executive vice president, operations. Nelson will lead efforts to scale AppHarvest’s network of farms and to build manufacturing and supply chain capability to ensure efficient delivery of consistent, high-quality products to major grocers and restaurants.
“Julie’s deep experience optimizing complex manufacturing and distribution networks for major consumer goods companies and her proven ability to drive productivity across the supply chain will help us to deliver improved profitability as we scale,” said AppHarvest President David Lee.
Nelson will play an integral role as an executive management committee member, reporting to President David Lee, and will aid in developing company strategy, establishing operations and driving efficiency to reach productivity and cost goals while ensuring quality and customer satisfaction.
“Julie has battleground-tested experience in scaling operations across sites,” said AppHarvest Founder & CEO Jonathan Webb. “Her recent focus on improving sustainability in the food and beverage supply chain by reducing food waste, energy consumption and greenhouse gas emissions makes her a natural fit at AppHarvest.”
Nelson joins AppHarvest most recently from McKinsey & Company, following a long tenure with PepsiCo, where she led supply chain teams in the North American beverage business and the global operations team. Her focus areas included network optimization, scaling new digital technologies and end-to-end value chain productivity.
“AppHarvest’s mission aligns with my personal values,” Nelson said. “AppHarvest’s vision of combining the best that nature offers boosted with world-class technology to sustainably and affordably grow nutritious fruits and vegetables is inspiring, and I look forward to building a best-in-class operational team in support of this mission to build a climate-resilient food supply.”
Nelson holds a bachelor of science in economics from the Wharton School of the University of Pennsylvania and an MBA from Harvard Business School. She is an advisory council member for the West Virginia University Global Supply Chain Management Program.
About AppHarvest
AppHarvest is an applied technology company in Appalachia developing and operating some of the world’s largest high-tech indoor farms, designed to grow non-GMO, chemical pesticide-free produce, using up to 90 percent less water than open-field agriculture and only recycled rainwater while producing yields up to 30 times that of traditional agriculture on the same amount of land without agricultural runoff. The company combines the best that nature offers boosted with world-class technology including artificial intelligence and robotics to improve access for all to nutritious food, farming more sustainably, building a domestic food supply, and increasing investment in Appalachia. The company’s 60-acre Morehead, Ky. facility is among the largest indoor farms in the U.S. For more information, visit https://www.appharvest.com/.
MEDIA CONTACTS: Travis Parman, Travis.Parman@appharvest.com;
Blair Carpenter, Blair.Carpenter@appharvest.com
IMAGE/VIDEO GALLERY: Available here
Lead Photo: Julie Nelson will be joining AppHarvest as its executive vice president, operations.
Converting Urban Areas Into Indoor Pesticide-Free Farms For Year-Round Food
Indoor farming addresses the concern of limited arable land and water wastage. In vertical farming, the need for land can be reduced by a hundred-fold, and by recirculating and reusing water, an average of 95% less water is required for growing the same crops when compared to outdoor farming
By Li Yap
July 14, 2021
Concerns With Traditional Farming
Traditional farms typically rely on herbicides, pesticides and fertilizers to grow crops, which can pollute the environment if used in excess. Up to 98% of a chemical spray will bounce off a crop instead of staying on the plant, resulting in chemicals accumulating in the soil and, eventually, waterways.
Biodiversity loss is another concern of conventional farming as the conversion of wild spaces to farmland has resulted in less space for wild plants and animals to live in. With the global population predicted to reach 9.7 billion by 2050, the agriculture industry is under pressure to scale up to meet these demands, which could potentially affect the natural environment further if nothing is done to rethink current farming practices.
With 40% of available global land already occupied by fields of crops and pastures for animals, it would be difficult to completely eliminate the impact that farms have on the natural environment. However, part of the answer could lie in indoor farming where growing conditions can be better managed, reducing the environmental impact of growing produce.
Indoor Farming Technology Market
The indoor farming technology market was valued at $14.5 billion in 2020 and is projected to reach $24.8 billion by 2026.
The contained facilities used in indoor farming allow farmers to better control and optimize growing conditions. This results in higher yields compared to traditional farming methods whilst using less land area. For example, the average yield of tomatoes grown using traditional methods was reported in 2016 to be 1.85 pounds per square foot, while the average yield of tomatoes grown from greenhouse hydroponics was 10.59 pounds per square foot. By increasing the growing area by stacking additional planting layers, the overall crop yield can be increased.
Indoor farming addresses the concern of limited arable land and water wastage. In vertical farming, the need for land can be reduced by a hundred-fold, and by recirculating and reusing water, an average of 95% less water is required for growing the same crops when compared to outdoor farming.
Vertical farming is one of the techniques used to grow crops within indoor environments. By using artificial light and vertical growing systems such as aeroponics, aquaponics and hydroponics, crops such as kale, lettuce, strawberries and herbs can be grown within a clinically clean indoor system without the need for soil, sunlight and pesticides. This technology allows vertical farms to be set up close to populous areas or urban hubs, where harvests can be distributed locally.
80 Acres Farms
80 Acres Farms operates vertical farms in eight locations across four states. Its farms produce crops using zero pesticides and consume 97% less water compared to traditional farms.
Using 100% renewable energy and being completely indoors, 80 Acres’ operation is capable of producing various crop varieties all year without the need to rely on favorable weather.
Sophisticated technologies, including AI sensors, are incorporated into its operation to ensure that growth environments are optimized according to the plants’ genetics and that harvests are at the peak of ripeness. By relying on a smaller delivery radius, customers are able to access the produce within a day of picking.
“80 Acres' farms are, on average, 300 to 400 times more productive than field farming”, says co-founder Mike Zelkind. This is due to the vertical structures used for growing produce, which allows room for more crops in less space as well as faster-growing produce.
Current Limitations of Indoor Farming
Apart from the high energy costs associated with operating vertical farms, there are also high investment costs for urban land and for the technologies and devices needed to carefully control and monitor the growing environment – these include aspects such as temperature, lighting, and pollination.
The high initial investment compared with traditional farming is a drawback for indoor farms, but this also invites the opportunity for innovation and the development of more cost-effective technologies.
Transforming Agriculture for the Future
Transforming farming in a way that does not affect the natural environment will be no small task, given the sheer scale of the world’s agriculture. With a growing demand for food, there is an ever-increasing pressure for high-yielding and sustainable farming techniques.
In addition to being a great use of spaces not traditionally utilized for agriculture, the high yields of pesticide-free indoor farms show great promise. Although indoor farming is unlikely to completely replace traditional field farming right now, it still has the potential to answer, at least in part, the question about food security in the years to come.
Lead Photo: With the ever-growing demand for food placing increased pressure on the Earth’s resources, innovators are re-examining the fundamentals of farming to create a new and sustainable food system. With the hopes of potentially transforming global food systems, many emerging start-ups have identified urban indoor farming as a viable alternative to conventional farming.
mage Credit: Nikolay_E/Shutterstock.com
Video Credit: 80 Acres Farms/YouTube.com
Grōv Technologies Signs Definitive Agreement With Superior Farms
Agtech and indoor farming company, Grōv Technologies, today announced a definitive agreement with California-based Superior Farms for the purchase of 10 Olympus Tower Farms that will produce fresh year-round feed for Superior’s upcoming Sheep Discovery Center™ in Central Utah
July 12, 2021
Vineyard — Agtech and indoor farming company, Grōv Technologies, today announced a definitive agreement with California-based Superior Farms for the purchase of 10 Olympus Tower Farms that will produce fresh year-round feed for Superior’s upcoming Sheep Discovery Center™ in Central Utah. Grōv is part of Superior Farms’ efforts to dramatically improve the sustainability and growth of US lamb production.
The ten Olympus Tower Farms will produce 60,000 pounds of Grōv’s fresh High-Density Nutrient (HDN) Superfeed wheatgrass a day using less than 5 percent of the water needed for field-grown fodder, without the use of pesticides or herbicides.
The Sheep Discovery Center is a new venture of Superior Farms. The goal of the Discovery Center is to showcase how sustainably focused science and technology can help farmers increase their flocks and consistently produce high-quality lamb.
“Our collaboration with Superior showcases how Grōv indoor ag technology can benefit farmers who want to improve production and sustainability, and minimize risk, especially as it relates to drought conditions that plague regions across the world,” says Steve Lindsley, president of Grōv Technologies. “The innovative thinking of Superior Farms is right in line with our efforts to provide feed security for animals and food security for growing populations.”
Leveraging Grōv’s indoor Olympus Tower Farms to grow fresh HDN feed, Superior Farms intends to optimize nutrition and environmental conditions to help support animal health during the lambing cycle. Superior Farms will also implement Grōv’s seasonal lighting technology as part of Superior’s efforts to improve the productivity of their sheep and provide a more consistent lamb supply throughout the year.
“The current Western U.S. megadrought is pushing farmers to ration their natural resources and find innovative ways to give their animals a more sustainable and nutrient-rich environment,” says Rick Stott, CEO of Superior Farms. “Feeding sheep with Grōv HDN opens up new opportunities for sheep farmers and gives them a way to overcome the water issues affecting their flocks.”
During the Covid pandemic, more consumers tried lamb for the first time and continued to purchase it throughout the year. The US lamb industry expects demand to keep rising as the number of new consumers who are more familiar with lamb continues to grow.
For more information about Grōv Technologies please visit www.Grōvtech.com.
About Grōv Technologies, LLC
Grōv Technologies is pioneering next-generation indoor agriculture technology and science to help meet the demand for global food and animal feed security. The company has developed enterprise-scale, automated controlled environment agriculture (CEA) systems to grow high-density nutrient animal feed and other crops using significantly less water and resources than traditional farming. These systems utilize patented low-heat LED technology, seed-to-harvest robotics, and data-driven scientifically proven indoor growing protocols. Grōv also operates an LED lighting and power management subsidiary, Stellar Smart Energy Solutions, using proprietary Wave Power Transformation and power management networking technology for commercial and agricultural facilities. Grōv is wholly owned by Nu Skin Enterprises, Inc. (NYSE: NUS), which develops and distributes a comprehensive line of premium-quality beauty and wellness solutions through a global network of sales leaders.
About Superior Farms
Superior Farms, the leading purveyor of sustainably raised, ranch-to-table American lamb. Proudly providing the highest quality natural lamb for a variety of recipes from weeknight dinners to Sunday brunch, lunches, and more, Superior Farms offers a range of premium cuts. From the mountains of Utah, the brisk winters of Minnesota, and the shores of California, Superior Farms prides itself on working exclusively with family ranchers who raise lambs with the best care and commitment to quality wellbeing and stable environment. Respecting a nutrient-rich land, maintaining a sustainable footprint, and working with dedicated family ranchers who raise flocks with the highest level of care, all are core values that make Superior Farms the leader in American lamb. From the plant floor to the corner office, Superior Farms is also proud to be 100 percent owned by its dedicated and talented employees. For more information, visit www.superiorfarms.com, order home delivery at www.superior-farms.com, or follow the brand on Instagram (@SuperiorFarms) and Facebook (@SuperiorFarms).
Indoor Farming Is In Growth Mode
The future of indoor farming, including vertical farming, has nowhere to go but up. With parallel and perhaps inevitably colliding trends of sustainability, plant-based eating, food safety and labor-saving agricultural practices, produce grown in controlled environments is likely to become much more common in grocery stores.
By Lynn Petrak
July 9, 2021
The future of indoor farming, including vertical farming, has nowhere to go but up. With parallel and perhaps inevitably colliding trends of sustainability, plant-based eating, food safety and labor-saving agricultural practices, produce grown in controlled environments is likely to become much more common in grocery stores.
As a testament to the sunny future of the ag tech niche, the U.S. Department of Agriculture started a new Office of Urban Agriculture and Innovative Production last year. More than $3 million in initial grants were made available through that department in 2020.
Prognosticators have weighed in on a future of food that includes strategically located indoor farms throughout the country. In a report released late last year, Allied Market Research, whose Americas office is in Portland, Ore., projected that the global vertical-farming industry is expected to reach $1.38 billion by 2027, with a compound annual growth rate (CAGR) of 26.2% from 2021 to 2027.
Several grocers are already buying into this type of produce supply. Earlier this year, The Kroger Co., based in Cincinnati, began sourcing fresh produce from Hamilton, Ohio-based indoor grower 80 Acres Farms for the retailer’s stores in Ohio, Indiana and Kentucky. In 2020, Kroger partnered with German startup Infarm to add modular vertical farms to two of its Quality Food Centers in the Seattle area.
Also last year, Publix Super Markets said that it will invest more in hydroponic produce and added a new on-site trailer farm from a local hydroponic grower to its GreenWise Market store in the grocer’s hometown of Lakeland, Fla. Boise, Idaho-based Albertsons Cos. has collaborated with South San Francisco, Calif.-based Plenty and with Bowery Farming, based in New York, to provide its shoppers with fresh produce grown indoors. Natural and organic retailer Whole Foods Market, based in Austin, Texas, recently added a mini-farm from New York-based Farm.One to one of its Big Apple stores to provide herbs for prepared pizzas and drinks. In addition to these and other large grocery players, smaller chains and independents have teamed up with various greenhouses and growing operations near their locations.
Consumers have expressed their opinions about produce grown indoors. According to the 2021 “Power of Produce” report published by Arlington, Va.-based FMI – The Food Industry Association, and conducted by San Antonio-based 210 Analytics, 43% of shoppers don’t have a preference for produce coming from indoor versus outdoor farms. Those most likely to prefer indoor growing include urbanites, consumers with above-average spend per person, members of the Generation Z age demographic, higher-income households, core value-added shoppers, organic produce buyers and men. Those more likely to prefer outdoor-grown produce include consumers in rural areas and conventional produce buyers, the report found.
AeroFarms uses aeroponic methods to grow healthy plants, using up to 95% less water and no pesticides.
Greener Pastures
One of the biggest drivers of the move to produce more food in indoor-farming facilities is sustainability. From an environmental standpoint, indoor-grown produce may be part choice, part necessity, depending on the area and the circumstances.
Necessity is born of conditions wrought by continual weather extremes that are often attributed to a changing climate. Unusual weather patterns resulting in droughts, floods, storm damage and harmful freezes take a toll on traditional farms and on the farmers who grow fresh fruits and vegetables.
Weather extremes have always happened, but are becoming more frequent. For example, coming off last summer’s devastating derecho event, a drought that began in late 2020 in Iowa and has continued through early summer is stressing that state’s corn and soybean crops. Earlier this year, rare heavy snow, ice and frigid temperatures in Texas hurt winter wheat and some citrus crops.
At the same time, there’s an overall push to produce food in a more sustainable way. More than two-thirds (64%) of American consumers say that they’re willing to pay a premium for environmentally friendly products. “There is a trend – not a fad – of consumers who appreciate the benefit of getting produce soon after it’s harvested,” says David Rosenberg, co-founder and CEO of vertical-farming leader AeroFarms, based in Newark, N.J., “and more and more customers are realizing that they want products with no pesticides, because those are not meant for human beings.”
On the business side, sustainability is a central part of many CPGs’ and grocers’ corporate- responsibility platforms as they pledge to reduce their use of resources like water and energy. Many manufacturers and retailers have also revealed goals to cut down on or eliminate the use of pesticides in their products.
Other Seeds of Change
In addition to the pursuit of sustainable growing practices, other factors are contributing to interest in this method of agriculture. The need to shore up food security in the face of a booming global population and the problem of urban food deserts are notable catalysts. So is consumers’ penchant for eating more fresh plant-based foods, and foods grown in a more sustainable way.
Meanwhile, as evidenced in ubiquitous “Now hiring” signs, it can be tough to find workers to plant, care for and harvest crops. Indoor farms run with several automated controls and tasks are less affected by fluctuations and stresses in the labor market.
The global COVID-19 pandemic also contributed to the acceleration of indoor farming. When some retailers faced supply chain issues and had difficulty sourcing fresh products, they turned to new vendor partners that operated indoor farms with more controlled conditions and inventories. Indoor farms typically can be built faster and are also versatile operations that allow for pivots in the event of changing circumstances.
There are additional practical reasons for sourcing produce from indoor growers. “Right now, retailers want consistency in price, quality and delivery. At its core, we are delivering consistency,” notes Rosenberg, citing other profit-driven benefits such as reduced shrink and spoilage.
Modern indoor farms combine technology and agriculture to provide fresh produce in a more sustainable way.
Indoor-Farm Tour
Generally, plants in indoor-farming facilities are grown in cells stacked for space savings and efficiency. In lieu of the sun, LED lights are used to facilitate growth.
Watering techniques vary. In hydroponic farms, plant roots are placed in nutrient-rich solutions instead of soil. With aeroponics, exposed roots hang down from the plant and receive nutrients via a system that sprays nutrient-filled water.
Indoor farms take different forms in the United States and around the world. Some indoor farms are massive in size and almost industrial in their setup. Others are smaller and hyperlocal, using locations like repurposed shipping containers or greenhouses. Some farms are constructed vertically to minimize the physical footprint or to use existing buildings, while others are more spread out in their design. Farms are being built in urban areas, often in former manufacturing facilities, warehouses or multilevel stores, and in more rural areas, where they are run by longtime family farm owners who are looking for ways to reinvent their businesses in the wake of competition from big farms.
One thing is for sure: There are more of these types of growing operations. AeroFarms is one grower on the march, with a l36,000-square-foot aeroponics farm under construction in Virginia, set to be finished sometime in 2022.
In June, Vertical Roots, a Charleston, S.C.-based hydroponic container farm that’s part of Amplifed Ag, opened its third indoor farm in Atlanta at a facility run by two large produce suppliers in the Southeast. According to the company, the new farm will eliminate the need for transportation to the distributor and will enable produce to be delivered to local customers the same day that it’s harvested.
In mid-June, Morehead, Ky.-based grower AppHarvest revealed that it’s adding two large indoor farms in the Bluegrass State. With a completion date of the end of 2022, the farms will produce non-GMO leafy greens and fruits for shipment to grocers and restaurants.
Also in 2021, Irvington, N.Y.-based BrightFarms opened its newest indoor farm, in Hendersonville, N.C., a 6-acre greenhouse that will deliver to retailers in nearby areas in that state, as well as in South Carolina and Georgia.
Startup Bowery Farms is opening an R&D hub called “Farm X” that will help expand product development. The facility includes a new sensory lab and innovation center.
In another sign of the health of this sector, there’s major seed money – no pun intended – going toward indoor farming. Berlin-based Infarm, for example, is said to be going public following a reported merger with Kernel Group Holdings Inc., of San Francisco. In May, Bowery Farming revealed a new round of funding to the tune of $300 million that lifted the company’s estimated value to about $2.3 billion. Indoor-farming company Gotham Greens, based in Brooklyn, N.Y., revealed $87 million in new funding in December 2020.
While indoor farms are expanding, crops produced in such facilities are expected to grow, too. Most ag tech companies currently produce leafy greens and herbs in hundreds of different varieties. Tomatoes are also grown hydroponically in many places. Better technologies and a greater collective knowledge are spurring innovations in other types of crops grown indoors in an eco-friendlier way. AppHarvest, for its part, is growing strawberries in one of its new locations, and vine crops in another.
Implications for the Retail Produce Section
More and different types of indoor farms are transforming agriculture – and the retail produce department. Since many of these products are packaged on site, supermarket produce sections now feature a greater mix of packaged and bulk items. Offerings like packaged salads and tomatoes also help define and elevate a brand, whether it’s a store brand or a grower brand.
Coming off a year in which consumers prepared more foods and experimented with new products and varieties, several new products grown in indoor-farming facilities have hit the marketplace. Medford, Minn.-based Revol Greens recently rolled out new varieties of chopped romaine salads made with lettuces grown at its indoor farm in its home state. Revolution Farms, in Caledonia, Mich., is launching four new salad mixes. One of Bowery Farming’s latest products is a new Bowery Crispy Leaf Lettuce, deemed to be a “reinvigorated version” of iceberg lettuce. And that’s just the tip of the iceberg (lettuce).
Grocers can merchandise indoor-farmed produce in a creative way to distinguish their offerings and connect with shoppers. “We’ve worked in a process of co-creating with retailers,” observes AeroFarms’ Rosenberg. “It is an opportunity to deliver innovation and excitement for an exciting category.”
Lead Photo: Hydroponic farming company Vertical Roots is growing its footprint with a new indoor lettuce farm in the Atlanta area.
Ikea’s Hydroponic System Allows You To Grow Vegetables All Year Round Without A Garden…
Ikea’s indoor garden system is the perfect option for those who wish to grow their own food all year round but don’t have the garden space to be able to do it. Ikea’s indoor hydroponic garden allows anyone to grow fresh produce at home without the need for soil or any previous gardening experience.
Ikea’s indoor garden system is the perfect option for those who wish to grow their own food all year round but don’t have the garden space to be able to do it. Ikea’s indoor hydroponic garden allows anyone to grow fresh produce at home without the need for soil or any previous gardening experience.
The hydroponic system of the garden means that adequate light and water are everything that is needed to grow the plants successfully, meaning that there is no need for soil. Many of the vegetables that are widely available today are grown using this method.
The absorbent foam plugs that come with the Ikea system enable the seeds to sprout and then proceed to keep the seeds moist without over-watering them. Following the germination of the seeds, all that needs to be done is to transfer the entire foam plug into its own separate small pot and fill it with pumice stones, which can retain a lot of water…
The pots can then be transferred to a growing tray that is equipped with a solar lamp, which will provide the plants with enough nourishment to last all year round. The system is so efficient that it can even be successful in rooms without any sunlight, although they can be placed on a windowsill that gets a lot of sun if it is convenient.
The growing tray is additionally equipped with a built-in water sensor, which ensures that the plants are given the perfect amount of water. Helena Karlén, from the Swedish University of Agricultural Sciences, said, “The challenge was to make growing plants in a hydroponic system simple, so that anyone could succeed…”
Named in the KRYDDA/VÄXER series, the design was born out of a collaboration with agricultural scientists in Sweden, with a target audience of those who live in apartments or don’t have a garden, as well as people who want completely fresh produce even during the cold winter months.
Whilst the system is not the first indoor hydroponic system, it is a more affordable option than most, and ideal for those with minimal space. It also fits with Ikea’s notably forward-thinking over the past few years, as they follow an eco-friendly trend towards sustainability (via TruthTheory).
If you like this idea, be sure to share it with your friends and inspire someone you know. Anything becomes possible with just a little inspiration…
After The Chaos of 2020, Will Indoor Farming Be In Our Future?
“Rather than growing out in an outdoor field, we’re growing up,” says Forward Greens CEO and Founder, Ken Kaneko. “We’re able to control the temperature, the humidity, the airflow, as well as the lighting,” he says
VANCOUVER, Wash. — The year 2020 has forced a number of disruptions to our daily lives, so what if we have more years like it in the future? How will we make sure our communities can survive by getting vital resources, like food?
The answer may be growing inside an old Hewlett Packard plant at the Vancouver Tech Campus in Washington.
Forward Greens is probably not what you picture when you think “farm”: vertical floor to ceiling stacks of planters filled with microgreens and baby greens, growing under LED lights
Forward Greens, Vancouver, Wash.
“Rather than growing out in an outdoor field, we’re growing up,” says Forward Greens CEO and Founder, Ken Kaneko. “We’re able to control the temperature, the humidity, the airflow, as well as the lighting,” he says.
From arugula to kale to broccoli, everything growing inside this urban, indoor farm wouldn’t be growing outside on a chilly November day in the Pacific Northwest.
From start to finish, the whole process of farming is essentially done in one room. In just a week or two, the greens are on their way to grocery stores in Portland, Vancouver, and Seattle.
Kaneko, who had worked for Intel and more recently, Apple, founded Forward Greens in 2017 after a trip to Japan. There, he stumbled upon his first vertical farm.
“I thought, ‘man, it would be great if I can bring this back to the Pacific Northwest and essentially do it better, cheaper, and more efficiently,'” said Kaneko.
Kaneko says Forward Greens never uses any pesticides, fungicides or herbicides and it uses 95% less water and 99% less land than traditional outdoor farming. But, he says, it uses a lot of energy to power the lights.
“Any engineering problem has a balance of cost, time, environmental impact, but the whole mission of this business is to balance those in a positive way towards the environment,” Kaneko said.
So could this be the farming of the future?
OSU Professor of Horticulture, Gail Langellotto, is pretty certain that it’s not. “In the near future, I can’t imagine a future where only agriculture is indoor agriculture,” she says, pointing to the high start-up costs, the higher cost of labor, and the expensive and taxing energy use.
She says traditional, outdoor farming will be difficult to replace because of the efficiency, precision and scale the industry has mastered and is constantly improving.
But Langellotto adds that if we have more years like 2020, with the pandemic and destructive wildfires on top of climate change, indoor farming will be an asset. She says urban farming is robust to disruptions in the local food system.
“If there are some supply and transport issues that delay or limit the amount of food that can be brought into urban areas from more rural, further out regions, then you already have an urban food production system in the proximity of where the majority of people live,” Langellotto said.
Kaneko is encouraged by the fact that urban farms can be a huge asset, saying, “we don’t know what’s going to happen with respect to the wildfires, the pandemic, the climate, so we’re able to provide local and sustainable food regardless of all those parameters.”
And that may be why Kaneko says demand for indoor farms is increasing. In fact, he’s expanding and doubling production at the Vancouver location in the next couple months. But he’s looking even further ahead to an even brighter future.
He hopes to put a Forward Greens in every metropolitan area, so we don’t fall to the fate of those HP printers that used to be built where his plants now grow.
KATU2 ABC Forward Greens
by Wesleigh Ogle, Thursday, December 3rd 2020
Published by Dani Kliegerman, iGrow News
Nature Fresh Farms Wins Presidents Choice Fresh Product of The Year Award
Each year the award is distributed by Loblaw Companies Limited to one of their nominees. The criteria requires the product to be unique and stand alone as first to market in Canada, additionally, it must be a commercial success
Leamington, ON (November 25, 2020) – This year Nature Fresh Farms proudly accepted the PC Fresh Product of the Year Award for their Ontario Greenhouse Mixiany Cherry Tomatoes.
Each year the award is distributed by Loblaw Companies Limited to one of their nominees. The criteria requires the product to be unique and stand alone as first to market in Canada, additionally, it must be a commercial success, that is, it needed to have generated further sales and profit, thus having a major impact on the category for the period. The winner is determined by a ballot vote by colleagues of Loblaw Companies Ltd, with the award being presented virtually this year.
“We are honored and excited to receive this award as it truly is a testament to our team’s commitment to research and development,” said Vice President John Ketler. “Innovation is an integral part of the Nature Fresh Farms identity and thanks to our Discovery Center we are able to bring fresh flavorful product, like our Mixiany Tomatoes, to market.”
The Mixiany Cherry Tomatoes were performing very well in their research trials and were officially launched in Spring of 2020. This is a significant accomplishment for Nature Fresh Farms as the criteria for the award covered products launched between Fall 2017 to Summer 2020.
“We’d like to thank the entire LBL-PC team for their support and confidence in our product,” shared Director of Sales, Matt Quiring. “Our Mixiany Cherry Tomatoes is just one example of how our devotion to quality and flavor is reflected in our products and it is extremely rewarding to see it received so well by both Loblaws and our consumers.”
Nature Fresh Farms research team works hard at identifying these new varieties that taste exceptional and continue to look for new opportunities to offer more products to consumers. PC Greenhouse Mixiany is available in supermarkets owned and operated by Loblaw Companies Ltd and can be found in Ontario, Quebec and The East.
-30-
About Nature Fresh Farms -
Continuously expanding, Nature Fresh Farms has become one of the largest independent, vertically integrated greenhouse vegetable farms in North America. As a year-round grower with farms in Leamington, ON, Delta, OH, and Mexico, Nature Fresh Farms prides itself on consistently delivering exceptional flavor and quality to key retailers throughout North America, while continuing to innovate and introduce more viable and sustainable growing and packaging solutions.
SOURCE: Nature Fresh Farms | info@naturefresh.ca T: 519 326 1111 | www.naturefresh.ca
SINGAPORE: High-Five: Developing “The World’s First Vertical Aquaculture Farm”
Singapore-based entrepreneur John Diener is committed to developing a series of urban aquaculture facilities that are able to produce shrimp, whitefish and seaweeds in high tech five-story farming systems
by Rob Fletcher
24 November 2020
Singapore-based entrepreneur John Diener is committed to developing a series of urban aquaculture facilities that are able to produce shrimp, whitefish, and seaweeds in high tech five-story farming systems.
John Diener aims to produce shrimp, tilapia, and seaweeds in five-tier facilities that can be fitted into the footprint of a standard warehouse. © Akualogix
The last decade of Diener’s career has seen him involved in a number of aquaculture-related ventures, as well as agritech startups, and the concept of a completely novel farming system came to him in 2016 when he was researching how machine learning could benefit aquaculture during a part-time MSc in aquaculture at St Andrews University.
“I have a lot of experience in data science and I wanted to find out what would happen if you reassessed the whole concept of aquaculture,” he explains.
Diener’s research led him to believe that vertical farms using cutting-edge technologies had the capacity to produce – for their footprint – an impressive amount of seafood, making them suitable for urban settings.
Three pillars
Diener describes the development of the system as resting on three pillars – biological, mechanical and digital. The biological side relates to investigating the most productive integrated-multitrophic (IMTA) system, with vannamei shrimp as the primary species.
“The business plan has been developed around shrimp – they’re a unique product in terms of their flavour profile, much like salmon are, which makes it very hard to produce substitutes. And they can also be raised at high densities,” Diener notes.
“We’ve also incorporated a filter-feeding fish – we’re currently using tilapia because they’re very robust, but will probably trial milkfish too,” he adds.
The bottom of the IMTA pyramid is taken up by sea grapes – called umibudo in Japan, where they are considered something of a delicacy.
“These are known as ‘the green caviar’ in parts of Asia, so have the potential to be sold as food. They can also be used as an ingredient in shrimp feeds, as we’re aiming to produce our own, sustainable feeds, while they also help to remove nitrates and phosphates from the water,” says Diener.
Technology
The second pillar consists of the engineering, and Diener intends to develop raceway systems four or five levels high, which are equipped with modular autonomous devices to optimise factors such as measuring water quality. The third pillar relates to the digital side of operations.
“We’re investing time and effort to develop advanced technology to manage feeding – both in terms of studying shrimp behaviour so we know when to feed and in terms of measuring the biomass in the systems, so we know how much to feed. We will also be looking to manage the water quality by feeding information into a deep learning algorithm that can control factors like pump speeds and the addition of minerals to the water,” he says.
The digital side also covers the farm’s “Aqua OS” [operational systems], ensuring all the technology works together, to simplify the management of all the tanks, Diener explains.
Launch
John Diener, founder of Akualogix
Four years after coming up with the concept Diener launched his own company, called Akualogix, in August, after finding a suitable site for a pilot-scale facility, in a building owned by the Marine Aquaculture Centre, on St John’s island in Singapore. This will, he notes, be perfect for securing proof-of-concept, before he looks to expand into a commercial-scale facility.
Initially self-funded, by Diener and the company’s co-founder, they are now looking into securing pre-series A funding in order to build a larger scale production unit.
Funding opportunities have remained robust in the agri-food sector, despite the outbreak of Covid. And as our systems are designed for an urban environment, and food security is increasingly important in Singapore and other cities around the world, we see strong investor interest
“Funding opportunities have remained robust in the agri-food sector, despite the outbreak of Covid. And as our systems are designed for an urban environment, and food security is increasingly important in Singapore and other cities around the world, we see strong investor interest,” Diener reflects.
The current farm has – he predicts – the capacity to produce 500-600 kg of shrimp per cycle, but he’s not yet sure what the yields of the tilapia or sea grapes will be – pointing out that no one has undertaken a mass balance study in such a system.
A juvenile shrimp at the pilot facility in Singapore. © Akualogix
“Our business economics is based on shrimp – making any money from the tilapia would be the icing on the cake – but the main reason we have the fish is part of the multi-trophic system and benefit the overall environment, they’re part of the filtration system,” he explains.
We will be looking at establishing commercial farms that can produce in the region of 1,000 to 1,500 tonnes of shrimp a year. It might not sound like much compared to some of the commercial salmon RAS that are now being established, but if we’re operating 20 or 30 farms that would make us one of the biggest shrimp producers in the world
Next steps
Once the pilot facility has fulfilled its potential Diener aims to establish a farm – and ultimately a network of farms – that use Akualogix’s design and equipment, establishing partnerships in a range of countries, primarily in Asia, as the concept takes off.
“We will be looking at establishing commercial farms that can produce in the region of 1,000 to 1,500 tonnes of shrimp a year. It might not sound like much compared to some of the commercial salmon RAS that are now being established, but if we’re operating 20 or 30 farms that would make us one of the biggest shrimp producers in the world,” he points out.
Diener is also looking to develop a unique, sustainable feed that’s designed specifically for producing shrimp in RAS facilities.
“The current range of commercial shrimp feeds are not great for use in RAS, and we’re looking to produce a next generation shrimp feed using sustainable ingredients. And we’re looking for a flavour enhancing additive as a finishing diet – potentially one that comes from algae,” he says.
Given the technology involved and the emphasis on sustainable feed ingredients Diener is aware that production costs are going to be considerably higher than conventional shrimp farms.
“We estimate that our cost of production will be 40-50 percent higher than shrimp produced in a pond in, say, India. But we’re close to market and can charge a premium for a fresh product that’s so sustainably produced,” he says.
Operational experience
The pilot facility holds 30,000 shrimp per cohort and 1,000 tilapia. The former are housed in a two-stage grow-out system and he aims to take them from the end of the nursery stage to harvest in 60 days, while achieving survival rates of roughly 90 percent.
However, as Diener admits, the design concepts of the system are still evolving, and there are other issues that have caused setbacks.
“It turned out that our first batch of PL [post-larvae] had pathogenic vibrio and we started seeing mortalities related to vibriosis,” he explains.
It was an unfortunate start, but a useful reminder of the importance of biosecurity.
“We decided to implement a full biosecurity package [once operating commercially], which will include our own hatcheries to prevent the introduction of pathogens,” he says.
Should the pilot facility prove productive, and investment forthcoming, Diener then aims to roll out the concept across some of Asia’s most populous coastal cities.
“There’s currently a lot of investment in salmon RAS and I think shrimp are the next species to go in that direction. If we can be a pioneer of shrimp RAS it will be a game-changer,” he concludes.
D.I.Y. Microgreens You Can Grow On Your Kitchen Counter
Think of The Rewards of Cultivating
The Tastes of Summer All Through The winter. You Can Do This.
New to microgreens? Start with something in the mustard family (Brassicaceae) that offers a quick payoff, like arugula (shown), radish or mizuna (a mild-flavored mustard). Credit...Kate Spring
By Margaret Roach
Nov. 18, 2020
Since Kate Spring and her husband, Edge Fuentes, founded Good Heart Farmstead in Vermont in 2013, she has cultivated not just mesclun, strawberries and tomatoes, but also the abundance of the patience required of a farmer. Plant parenthood reminds us: Living things take time. And sometimes they have minds of their own.
Lately, as mother to Waylon, a 7-year-old son she calls “our best crop ever,” Ms. Spring is occasionally asked to dig down even deeper, in a growing test of wills — as she did after three long days of carrot harvest. “There are those moments, like when all those root vegetables need to be washed,” she said, “and your child commandeers the hose and washes you instead.”
But there is one crop, whose time is now, that promises near-instant gratification, requiring little patience and exhibiting blessedly minimal rebellion.
Microgreens — fully developed seed leaves or cotyledons plus a true leaf or two, bigger than sprouts but smaller than baby greens — can be grown indoors in a small space, making them the ideal off-season do-it-yourself project for those who miss the vegetable garden and its in-season flavors. By investing a couple of weeks in each tray of tiny, leafy greens, root vegetables or herbs, you can enliven winter with concentrated bursts of nutrition and taste.
In the garden off-season, freshly harvested basil microgreens grown indoors punch up the summery quotient when Kate Spring, an owner of Good Heart Farmstead, serves red sauce she cooked and froze at peak tomato harvest. Credit...Kate Spring
Microgreens are a cusp-season crop at Good Heart Farmstead, an L3C, or low-profit limited-liability corporation, which means it’s “a mix between a nonprofit and for-profit business — a for-profit but with a social mission in the forefront,” Ms. Spring said. “We work on increasing food access for low-income Vermonters,” often in collaboration with the Northeast Organic Farming Association of Vermont.
The small, certified-organic operation in Worcester (Zone 4a) focuses on farm shares, or CSA subscriptions, serving up to 100 subscribers in the summer season, one of four subscription periods each year.
As the last outdoor fall greens fade, Ms. Spring and Mr. Fuentes sow microgreens in greenhouse flats to add “a nice, fresh green item in the share,” she said, that is otherwise transitioning to roots and other winter storage vegetables.
So order some seed, clear a space on the kitchen counter and call the seed-starting light into service. It’s microgreen season.
Larger seed for microgreens like chard and beets can be scattered on a level surface of an inch and a half of tamped-down, seed-starting soil, with about six to eight seeds per square inch. Credit...Kate Spring
Why Grow Microgreens?
Besides the sheer awe inherent in any version of seed-starting, there are other motivating factors. Price, for instance.
Microgreens are what farmers refer to as a high-value crop. In plastic grocery-store clamshell boxes they may run $2 to $3 an ounce ($32 to $48 a pound) — “a really premium product,” Ms. Spring said.
Microgreens are also nutrient-dense. Researchers with the University of Maryland College of Agriculture and Natural Resources and the United States Department of Agriculture evaluated vitamin and carotenoid concentrations in a range of varieties in a 2012 paper. The findings, in brief: Microgreens contained up to 40 times the nutrients of the plants’ mature leaves.
And oh, the flavor. Yes, they brighten up salads and sandwiches, but cilantro microgreens on top of black bean and sweet potato tacos, anyone? They’re highly recommended by the Spring-Fuentes household, where there are always basil microgreens as well, for punching up the summery quotient of red sauce frozen at peak tomato harvest.
“Arugula or basil or kale microgreens are also really good on eggs in the morning,” said Ms. Spring, who tends to use them “as an additive, not the main ingredient.”
Organic field pea seeds will become pea shoots, a customer favorite at Good Heart Farmstead, in Vermont. They are sown very densely and pressed into the soil after the seeds are soaked overnight. Credit...Kate Spring
Start With These Varieties
The diversity of organic microgreen seed offerings in catalogs like Johnny’s Selected Seeds and High Mowing Organic Seeds can be intimidating. Start with something in the mustard family (Brassicaceae) that promises a quick payoff, Ms. Spring suggested, like radish, arugula or mizuna (a mild-flavored mustard).
“Our favorites are basil, cilantro, Red Russian kale and the arugula and mizuna,” Ms. Spring said.
Broccoli and chard are popular, too. Catalogs also offer mixes — like a spicy one of various mustards, selected to germinate and mature on a similar timeline.
While the fields are resting, there are usually microgreens growing on Good Heart Farmstead’s greenhouse benches, to add a fresh, green item to the wintertime CSA shares. Credit...Kate Spring
The Gear
Yes, you can upcycle a cardboard egg carton or plastic sushi container into seed-sowing service, and maybe that’s a good place to begin. But once you’re hooked, a couple of standard nursery flats with drainage holes, called 1020 flats, with trays that fit beneath, will optimize the process. (In the meantime, a plastic boot tray or a rimmed baking sheet could be called into action under ad hoc seedling trays.)
You’ll also need:
A spray bottle for watering (recommended: a one-hand pressure sprayer like the Solo 418)
A germination dome to fit your flats, or paper towels
A bag of seed-starting mix and a moisture-proof tub or other container to stash it in (after each harvest, the soil can be composted, and once the plant matter breaks down, reused two or three times)
A grow light with T5 high-output fluorescent tubes on an adjustable stand (microgreens grow faster and stronger with proper overhead light than they will on a windowsill)
A fan
And, of course, seeds
You can simply can upcycle a cardboard egg carton or plastic sushi container into seed-sowing service, but once you’re hooked, a couple of standard nursery flats with drainage holes, called 1020 flats, and trays that fit beneath will optimize the process. Credit...Kate Spring
Kate Spring’s Step-by-Step Instructions
There is no one-size-fits-all growing method. “It takes some guesswork and practice, so go into it with a trial mind,” Ms. Spring said.
Experimenting with varieties, sowing density and harvest timing — an extra day or two, a half-inch taller than the last batch? — will reveal what works for you.
Using more than one flat and tray will mean fewer gaps in your supply. You could try sowing a succession crop when the current one is within a few days of harvest, or sowing slower- and faster-growing varieties at the same time.
The key is taking notes and researching the catalog websites, where the “number of days to first true leaf” will indicate how fast one variety will grow relative to another. That is especially important if you want to grow partial flats of two things. A good match for a uniform harvest pairs crops with similar days to maturity — like broccoli and Red Russian kale (both 10 to 15 days to true leaf) or basil and cilantro (16 to 25 days).
Trays of microgreens at various stages of development in the Good Heart Farmstead greenhouse benefit from the circulation provided by a fan on low nearby, which helps prevent a fungal disease called damping off. Credit...Kate Spring
Start with the right location: 65 to 70 degrees, not adjacent to a heater or a drafty window. Moisten a supply of potting soil, either in its plastic bag or in a waterproof tub, by adding a small amount of water and mixing it with your hands or a trowel. Squeeze a fistful; it should be moist enough to hold its shape, but not so wet that water drips out.
Then line your tray with an inch or so of soil, tamped down so it’s compact, with an even surface. This will help ensure that seeds have equal soil contact for even germination.
To sow the seeds, scatter them thickly, according to the packet directions, aiming for 10 to 12 seeds per square inch for small seeds like basil, mizuna or kale and six to eight seeds for larger ones like beets or chard. Gently press them into the soil.
Lightly water the seeds with a mister or spray bottle.
Cover the tray with a germination dome or a damp paper towel. (If you use a paper towel, mist it daily so it stays moist during germination.) No supplemental light is needed yet.
As soon as the seeds germinate, usually in about three to five days, remove the dome or towel and place the uncovered tray under grow lights for 16 hours a day.
Water as needed to keep the soil moist but not waterlogged. Microgreens flatten easily, so use a mist or spray, or switch to bottom watering, adding a quarter of an inch of water to the tray below; the flat’s drainage holes will allow the soil to wick up water. For even watering, trays must be on a level surface.
Airflow is important, or thickly sown microgreens can suffer from a fungal disease called damping off. A fan set on low nearby helps.
Microgreens are harvested around the time the first true leaf appears — the one that resembles an older version of the plant, often between an inch or two tall. Use sharp scissors or a harvest knife (Johnny’s and High Moving both sell Victorinox serrated knives). Eat immediately or refrigerate in a closed plastic bag or container for two to three days.
Waylon, the son of Good Heart Farmstead owners Kate Spring and her husband, Edge Fuentes, is 7 years old and a lover of pea shoots and all things salad. This year, he grew his first garden. Credit...Kate Spring
Ready to Graduate to Pea Shoots?
Pea shoots, a CSA-subscriber favorite at Good Heart Farmstead, are grown indoors in spring from organic field pea seeds, a kind of pea used for cover-cropping beds to improve the soil.
There are subtle differences in the process, Ms. Spring said: “We soak the seeds overnight, so that they have a little head start, and we really pack them in there.”
After that, the seeds take 12 to 14 days to harvest, at two to four inches high. Ms. Spring likes them on the bigger side — as does Waylon, who has all too quickly gone from sprout to shoot stage himself, his mother noted.
Company Adds New Executive Leaders As It Becomes The Largest Vertical Farming Company In The U.S.
Bowery Farming, the Modern Farming Company, today announced that its fresh, traceable Protected Produce is now available in more than 650 U.S. stores — marking a rapid increase from 100 stores in January
StreetInsider.com
9/25/20201
Bowery Farming Announces Availability in 650 Stores,
Marking 600% Growth This Year
NEW YORK--(BUSINESS WIRE)-- Bowery Farming, the Modern Farming Company, today announced that its fresh, traceable Protected Produce is now available in more than 650 U.S. stores — marking a rapid increase from 100 stores in January. With this expansion, Bowery becomes the largest vertical farming company in the U.S. as consumers are hungry for flavorful, local, and sustainable food.
Bowery’s brick and mortar presence in the Mid-Atlantic and Northeast includes Whole Foods Market, Giant Food, Stop & Shop, Walmart, Weis Markets, and a number of specialty grocers. The company’s expansion has catalyzed more than 600% in-store sales growth since the beginning of this year and it has more than doubled sales with e-commerce partners.
Growing a New Generation of Greens
Located near the cities they serve, Bowery’s indoor farms use technology to create a simplified, agile food system focused on flavor, freshness, and safety — farming efficiently to feed locally. At the core of its farms is the BoweryOS, its proprietary operating system, which uses sensors, vision systems, machine learning, and automation technology to monitor and control all variables contributing to crop growth. By applying proprietary machine learning algorithms to environmental data, the BoweryOS determines the ideal recipe for each crop and makes automatic adjustments to conditions, such as temperature, humidity, airflow, light intensity, and nutrients to optimize crop quality, health, yield, and flavor, giving the plants exactly what they need, when they need it. Every farm benefits from the collective knowledge of the BoweryOS, making the entire network stronger with each new farm built.
As a result of the BoweryOS and the other systems built by Bowery, its farms are more than 100 times more productive on the same footprint of land than traditional agriculture, use a fraction of the water, and grow traceable pesticide-free produce. Bowery’s greens and herbs (such as Arugula, Crispy Leaf, Basil, and Butterhead) grow in completely controlled environments year-round, at least two times quicker than in a field — completely independent of weather and seasonality. Bowery produce is harvested at the peak of quality and taste and is available on the shelf within just a few days.
“Climate events continue to disrupt the way food is grown and distributed, and the pandemic exacerbated the vulnerabilities in our already fragile food system. We need a more resilient solution focused on the future, and that’s exactly what we’re building at Bowery,” says Irving Fain, Founder & CEO of Bowery Farming. “Our growth has been driven by consumer demand for safer and more transparently grown produce, and our ability to provide a consistent and reliable supply to our retail partners. We’re incredibly fortunate to have a dynamic team at Bowery that is relentlessly committed to innovation, strengthening our food system, and increasing access to fresh, healthy food.”
Cultivating Bowery Farming Talent
As the company continues to grow, it welcomes its first-ever Chief Supply Chain Officer, Colin Nelson, who will oversee Bowery’s end-to-end operations, from seed to store. A mechanical engineer by training, Nelson has spent the past 30 years of his career in supply chain management and operations at major multinationals, including Unilever and GlaxoSmithKline. Nelson most recently served as Senior Vice President and Global Chief Supply Chain Officer at Walgreens Boots Alliance, where he led supply chain management of retail and wholesale pharmaceuticals and front-end retail.
“I’m impressed by what Bowery is building and how the company is applying innovative technology and human ingenuity to strengthen our food system and help feed a growing urban population in an economically sustainable way,” said Colin Nelson, Chief Supply Chain Officer of Bowery Farming. “I am looking forward to working closely with the incredibly passionate, purpose-driven team to further expand the business and deliver excellent economics through the supply chain and operational efficiencies at Bowery.”
Nelson is the most recent among a series of strategic hires for Bowery, which also includes Carmela Cugini, Chief Revenue Officer (formerly Head of Merchandising & Curation at Jet.com and VP and General Manager of Walmart’s US e-commerce team) and Katie Seawell, Chief Marketing Officer (formerly SVP of Product and Marketing for Starbucks). The company has also added two new members to its Board of Directors: Sally Genster Robling (former EVP of Pinnacle Foods and founding President of the $1.1B Birds Eye Division) and Michael Lynton (Chairman of Snap Inc., and former Chairman and Chief Executive of Sony Pictures Entertainment).
“Bowery Farming’s best-in-class approach and application of software, robotics, automation, and AI has proven that local, smart farming at scale can be a reliable and more sustainable model for the future of agriculture,” said Hans Tung, Managing Partner at GGV Capital. “Solving for our global food challenge requires us to think differently about how we can address a number of issues — from climate events and biodiversity to population growth and public health — and Bowery’s multidisciplinary, technology-driven approach makes this possible.”
As consumers continue to seek healthy, safe, and sustainable food brands, Bowery expects more growth ahead. Already, indoor farming brands are outpacing conventional packaged salad in the grocery store by more than 25% compared to last year, according to IRI. And as online grocery shopping increases in popularity, Bowery is providing consumers with more options with e-commerce retailers, including Peapod and Amazon Fresh.
For more information about Bowery, please visit www.boweryfarming.com, and connect with the company on LinkedIn, Twitter, and Instagram.
About Bowery Farming
Bowery Farming, the Modern Farming Company was founded in 2015 with the belief that technology and human ingenuity can grow better food for a better future. By building smart indoor farms close to the cities they serve, Bowery creates the optimal conditions to cultivate wildly flavorful Protected Produce that’s available on the shelf just a few days after harvest.
Its proprietary software system, the BoweryOS, uses sensors, vision systems, automation technology, robotics, and machine learning to monitor plants and all the variables that drive their growth 24/7. Because Bowery controls the entire process from seed to store, farms grow produce year-round, ensuring a safer supply of food that’s reliable and consistent.
The farms are 100 times more productive on the same footprint of land than traditional agriculture, and grow traceable pesticide-free produce — the purest, best expression of what produce is meant to be — with a fraction of the water.
Bowery currently has three farms: a commercial farm and R&D Center of Excellence in Kearny, New Jersey, and a commercial farm in Nottingham, Maryland. The company serves more than 650 stores in the Tri-State area and Mid-Atlantic region, including Whole Foods Market, Giant Food, Stop & Shop, Weis, Walmart, and specialty grocers, along with online partners, such as Amazon Fresh, Hungryroot, and Peapod.
Based in New York City, the company has raised over $172.5 million from leading investors, including Temasek, GV (formerly Google Ventures), General Catalyst, GGV Capital, First Round Capital, Henry Kravis, Jeff Wilke, and Dara Khosrowshahi, as well as some of the foremost thought leaders in food, including Tom Colicchio, José Andres, and David Barber of Blue Hill.
For more information on Bowery and its products, please visit www.BoweryFarming.com
Press kit: https://boweryfarming.com/press/
View source version on businesswire.com:
https://www.businesswire.com/news/home/20200924005203/en/
Rachel Alkon
Press@BoweryFarming.com
Source: Bowery Farming
Little Leaf Farms Expands Hydroponic Greens Distribution Across East Coast
Based in Massachusetts, Little Leaf Farms has doubled its hydroponic greenhouse-growing capacity to 10 acres of fields under glass capable of producing more than two million packages of lettuce each month, which will broaden the company's distribution to retailers in New York, New Jersey, Pennsylvania, and South Carolina
15-Sep-2020
By Mary Ellen Shoup
Based in Massachusetts, Little Leaf Farms has doubled its hydroponic greenhouse-growing capacity to 10 acres of fields under glass capable of producing more than two million packages of lettuce each month, which will broaden the company's distribution to retailers in New York, New Jersey, Pennsylvania, and South Carolina.
Read More At: Food Navigator
California Wildfires And Food Security
The smoke from these fires are wreaking havoc to nearby farms, especially outdoor farms. The article lists the following negative impacts from poor quality, smoke-filled air
09-17-20
As wildfires ravage through the State of California, we at CO2 GRO offer our deepest sympathies to those who have been greatly affected.
According to this article by Growing Produce, “On the whole, the fires have not invaded growing fields. However, several growing areas lie close to the fires.” Hopefully, the fires can be controlled and farms spared.
However, the smoke from these fires are wreaking havoc to nearby farms, especially outdoor farms. The article lists the following negative impacts from poor quality, smoke-filled air:
With less sunlight reaching crops, crops develop more slowly.
Less sunlight can lead to higher disease loads. Obviously, when ash coats the leaves and fruit, crops have even less access to light.
Protecting workers delays harvest, leading to destroying overly ripe crops.
Some crops absorb enough smoke to change the flavor. During the 2018 fire season, several vineyards were unable to sell their grapes.
Protected Cultivation
While most outdoor growers will experience the negative impacts of smoke, protected cultivation facilities such as greenhouses have the ability to cope. LED lighting, frequent air exchange, protected structures and more environmental control enable greenhouses to provide their plants a more consistent environment for growth, despite the conditions outside. Protected structures also offer a safer environment for workers.
CO2 Gas Supply
CO2 gas supply shortages in California as a result of COVID-19 and now with fires causing several disruptions in the supply chain have hampered sealed greenhouses and indoor cultivation facilities. Supply has significantly slowed and prices have risen. Several cultivation facilities have temporarily stopped using CO2 gas for growing, thus hampering crop yields by up to 30%.
CO2 Delivery Solutions™
CO2 Delivery Solutions™ offers greenhouse and indoor growers the opportunity to supplement their plants with CO2 while using over 90% less gas versus traditional atmospheric enrichment. In difficult times like this being experienced in California, ensuring our food supply with the highest yields possible is paramount. Greenhouses and indoor cultivation facilities with optimal yield enhancing technologies that require minimal resources, such as CO2 Delivery Solutions™, provide food supply security to consumers while protecting growers’ people and profits.
CO2 Delivery Solutions™ also provides a method for sequestering CO2 gas by providing it as an input for plants to grow. Nearly all the CO2 provided to the plants through CO2 Delivery Solutions™ aqueous CO2 mist is sequestered by the plant. Unlike CO2 gassing in which approximately half the CO2 gas that is pumped into the grow room leaks back into the atmosphere.
For more information on CO2 Delivery Solutions™, watch this video and explore our website.
This Week On Green Sense Show: Controlled Environment Agriculture
Featuring innovators that are changing the world with their sustainable ideas
As the Coronavirus touches nearly every aspect of life in nearly every part of the world, how we raise food continues to innovate.
Hear the interview with our longtime correspondent Chris Higgins of Urban Ag news as he talks about the latest developments in indoor farming- greenhouses and vertical farms and how they are presenting a solution to the food supply chain during this pandemic. #verticalfarming #greenhouses #sustainability
VIDEO: IGS Intelligent System Design – FTS Finds Out More
IGS has, as a company, focused from the outset on automation, intelligent system design, and the energy equation of CEA vertical farming
July 6, 2020
IGS has, as a company, focused from the outset on automation, intelligent system design, and the energy equation of CEA vertical farming. This has garnered them a reputation as one of the leading and most innovative companies in the industry. We took some time to have a chat with them and find out a bit more about how this all works in practice.
FTS: Hello and thanks for taking the time to talk with us. Can you briefly introduce IGS, its history as well as its outlook?
IGS: IGS was founded in 2013 bringing together decades of farming and engineering experience with a vision to revolutionize the indoor growing market. The two founders, farmer Henry Aykroyd and our CTO Dave Scott had an appetite for innovation and realized that there were significant gaps in the provision of scalable technology for the sector.
Henry knew how to grow and understood the challenges which faced traditional farming: Dave knew how to manage automation and power controls in an industrial environment. The opportunity to bring greater climate control to a growing environment was significant. The ability to manage power consumption was revolutionary. The simplicity of its implementation and use is pivotal.
We opened our first vertical farm demonstrator in Scotland in 2018. Artificial intelligence determines optimal nutritional input and the exact combination or ‘recipes’ of weather: lighting, watering, and ventilation. Data is collected continuously and machine learning used to make iterative adjustments, all of which is monitored through a web-based app. The whole Intelligent Growth platform is IOT-enabled to automate system control and management. Our degree of control is so fine that each 6m2 growth tray has its own microclimate. Technical simplicity is at the heart of our mechanical design.
Our commitment to innovation has continued apace and we have evolved the applications of our technology beyond agriculture to create solutions for a wide variety of indoor environments, developing the Intelligent Grid platform.
The Intelligent Grid uses the same IOT-enabled power and controls platform to manage and monitor lights, sensors, cameras, and communications for complete climate control and reporting. It too has a very simple, clean, and elegant design for application in any commercial building, greenhouse or livestock shed. In contrast to the vertical farm, we use our same core technology through the Intelligent Grid to create whole-space macroclimates.
Both IGS demonstrators are based at the James Hutton Institute, a world-renowned crop, and plant science research facility. IGS and the Hutton collaborate closely to help advance the understanding of plant science for indoor growing.
Until 2018 IGS had invested approximately £7m in R&D to ensure that its platforms offered the greatest levels of control and achieved levels of economic viability, scale, and minimal environmental impact compared to other systems on the market. In 2019 IGS raised £7 million in institutional capital to enter production and take its systems to global markets. We continue to invest over £1m per annum in R&D.
FTS: You have recently shared news of two reseller partnerships – one in the Middle East and one in the UK and Italy with TEP Renewables. Can you tell us briefly a bit more about them?
IGS: We have been talking to International Real Estate Partners (IREP), the international facilities management firm for some time in the Middle East, and we’re really pleased to recently sign this referral agreement which is specifically focused on indoor vertical farming for the UAE and Saudi Arabian markets.
We also have an opportunity to extend into Asian markets in the future. It gives us a greater capacity to service the Middle East market and secure and deploy vertical farming platforms across the region. IREP’s presence in this market is well established with many existing customers across agriculture, retail, and construction and it is a very positive development for both companies we believe.
The agreement with TEP Renewables is an MOU (Memorandum of Understanding) or a reseller-type partnership if we identify customers who would like to operate solar-powered vertical farms in Italy or the United Kingdom that we will work with them.
FTS: Fantastic! In the end, any vertical farm (indeed any farm!) is only as environmentally sustainable as its energy equations. But it is also only as financially sustainable as its energy cost. You have focused quite intensely on this energy cost question. As we see this dramatic collapse of fossil fuel energy production return on investment, it seems that NOW is the time to have renewable energy options on hand for CEA. Do you believe that renewable energy can be cost-competitive – both in terms of installation, sustainable life-cycle and with regard to the price of the final product for the consumer?
IGS: We consider a variety of power distribution and supply methods. Renewables can have considerable benefits from an environmental perspective and also specific to grants and other financial support for utilizing renewable energy resources.
The “virtual power plant” capabilities of our systems indicate strong Demand Side Response (DSR) potential. We can manipulate our growth cycles to respond to power availability and respond to inherent instabilities in power networks. This is already having an influence on our engagement in circular energy projects to utilize spare energy for growing and allows for more renewable power sources to be adopted.
FTS: Labor cost is the other biggest outlay for any vertical farm. You have invested heavily in automation. Is the trade-off of increased capital expenditure for automation worth the reduction in operational expenditure for labor, in your experience?
IGS: Absolutely. Driving down the farm gate price is the ultimate goal and while labor costs vary from region to region, we believe that this investment in the automation (and indeed the associated patents) within our growing operations is imperative and differentiates our systems considerably.
FTS: You’ve set about designing modular and intelligent systems. Such a bespoke system offers advantages of course, as we’ve seen above. But it can also present challenges if it cannot be integrated with other equipment and systems later. Do you future-proof your systems to be able to accommodate such updates and integrations over time?
IGS: We have thought about this from the outset, and our systems are designed in a plug and play model, rather than being bespoke as such. Scalability is paramount for our customers and this has been a consideration throughout our R&D development. Rather than using proprietary systems for processes such as sowing and harvesting, we use off-the-shelf equipment and components. This means we can keep startup and maintenance costs down by providing items with which farmers are already familiar. If a section of the vertical farming system needs to be replaced or upgraded, such as a water filter, a lighting panel or a tray, it can be done with almost no interruption.
However, what is also imperative to think about in terms of future proofing, and a hugely important part of our approach, is how we work so closely with the science community to better understand plant light interactions. The level of control we have designed into our hardware systems allows us to flex and adapt as we need to deploy the most up to date plant light information through our software development, which is continuously evolving.
The approach of our software development has also involved maximising security of our systems and ensuring simplicity of operation. This will be continuously updated, but with seamless integration for our customers.
FTS: Along with FTS, you’ve joined a number of other associations and similar collaborative groups. Why is this important to you as a company, and how do you balance the proprietary needs of your company against this desire to cooperate?
IGS: Collaboration and cooperation across this sector is essential. Our vision is that sustainable change will only be delivered not only when we collaborate, but when we are all open and honest about the limitations, as well as the opportunities for this sector. We want to work alongside technology vendors with complementary products, and with growers and producers, supported by science and greater understanding of growing plants indoors, all backed by far-sighted investors.
We firmly believe that through innovation, collaboration and investment we can create an economically and environmentally sustainable global indoor food industry.
FTS: Thanks so much for taking the time to talk with us today. We wish you every success and look forward to working with you in the future.
IGS: Thanks very much indeed. We look forward very much to be part of Farmtech Society as we all move forward in the development and innovation of agricultural technology.
For IGS
David Farquhar
CEO
Shipping Container Farms Come to London as Growers Ditch Soil
In the era of climate change and Brexit, British farming is facing unprecedented challenges. How to supply environmentally friendly, locally sourced, and competitively priced food?
Vegetables Are Grown Vertically Supplied With Nutrient-Rich Water
20 June 2020
Racks of vegetables grown in a shipping container in London CREDIT: Fiona Hanson
In the era of climate change and Brexit, British farming is facing unprecedented challenges. How to supply environmentally friendly, locally sourced, and competitively priced food?
One part of the answer could lie in a shipping container in an east London car park, just moment’s away from the capital’s business district. Inside are racks of leafy green vegetables, grown vertically using hydroponic technology. Instead of being planted in soil, the vegetables are plugged into a system of nutrient-rich water and kept at the optimal temperature, under specially designed lighting.
The result is flavorsome lettuces, kale, basil, and other leaves, free of pesticides and using up to 95 percent less water than traditional agriculture over a fraction of the space. The shipping containers, which are custom made, mean the produce can be located virtually on the doorstep of its market, effectively eliminating food miles.“
Traditional organic farming is not sustainable if we're going to feed a population,” says Sebastian Sainsbury, the founder of Crate to Plate, which has just had its first harvest.
Not only does Crate to Plate use otherwise wasted space - these three shipping containers can grow the equivalent of an acre’s soil - but the proximity to customers keeps the produce fresh.“ When you harvest the lettuce from the soil, within 48 hours, you've lost 40 percent of the nutritional value. And it goes down every day,”
Indoor farming has boomed in recent years, particularly in the US, where Mr. Sainsbury lived until recently and where he developed his business.
But the UK is yet to fully capitalize on its opportunities, says Dr. Robert Hancock of the James Hutton Institute, which is supporting pioneering vertical farming techniques from its facility in Dundee.“
Even with current technologies and current efficiencies, there's probably a lot more that can be done. And I think that indoor farming can interface a lot more with the broader agricultural picture,” he said.
Lead Farmer of Crate to Plate, a hydroponic vertical farm producing leafy greens and herbs.
CREDIT: Fiona Hanson
Environment Secretary George Eustice this week said vertical farming would have a vital role to play in helping British farming meet the challenges of climate change and post-Brexit food security.
“There are a lot of pressures on land use,” he told the parliamentary environment committee, highlighting “the tricky issue” of repairing biodiversity and soil health in our intensely farmed landscapes.
Mr. Hancock highlighted the UK’s strawberry industry, which relies on imports of propagated plants from the Netherlands, as one example of where indoor farming could boost British production. Britain produces just 7 percent of its fruit and 53 percent of its vegetables. But ultimately, he says, vertical farming can only ever be part of the answer and will likely be limited to salads, berries, and niche crops.
“The replacement for calorie crops I don't think is ever going to happen,” he said.
Crate to Plate is the latest of several hydroponic farming ventures started by those outside of traditional agriculture (Mr. Sainsbury is an ex-banker), many of which haven’t translated to long-term success. The key to seeing vertical farming at scale will be getting more existing farmers on board, says Mr. Hancock.“
They understand the economics of growing.
And they also understand the routes to market,” he said.
The government is hoping that the end of the EU's Common Agricultural Policy could be a chance for new blood to enter the agricultural industry, and will offer older farmers a “golden handshake” if they retire early.
Mr. Sainsbury employs three recent agricultural graduates and says the younger generation are eager to explore new technologies. He has also had interest from farmers keen to locate his shipping containers on their land.
So far, Crate to Plate’s economies of scale and niche produce puts them out of reach of the average supermarket shopper (think £10+ salads marketed to City workers). But they have hopes of moving into residential areas, amid a growing trend for urban farming. The dream, says Mr. Sainsbury, would be a vegetable farm in every urban neighborhood, manned by a dedicated farmer and producing fresh produce for everyone to buy.“
The aim is to make it as local as possible,” he said.
A Guide To Vertical Farming Techniques
If you don’t already, chances are you’ll be eating more produce from indoor farms in the near future. Learn what that means
If you don’t already, chances are you’ll be eating more produce from indoor farms in the near future. Learn what that means.
Our ancestors first learned to farm nearly 12,000 years ago. By cultivating and domesticating seeds, these once hunter-gatherers broke away from their nomadic lifestyles, settled down to produce controlled and reliable food sources (weather permitting, of course) and, little did they know, change the course of the planet’s future.
Fast forward to the 20th century when a group of architects started planning to alter food production in their own way. They aimed to decreased dependency on traditional land-based farms and harness spatial efficiency in our dense built environment; think less wide-open spaces with tractors and more structures growing stacked layers of crops. This practice—widely referred to as “indoor” or “vertical farming” (taken from Gilbert Ellis Bailey’s 1915 book of the same name)—is alive and booming today, and especially in the New York metro area.
Columbia University professor emeritus and ecologist Dickson Despommier helped to envision the modern vertical farm and indoor agriculture while teaching a graduate-level course in 1999. His students realized that simply using rooftop gardens would been grossly insufficient to feeding the population of Manhattan so inline with urban agriculture predecessors, he began researching different techniques and structures. Despommier is among several academics and vertical farming thought leaders who see vertical farming today as part of the answer to a range of global problems (many partly caused by agriculture) including climate change and water scarcity.
There are a lot of ways to farm indoors and below are three different soilless processes recommended by Despommier. Done properly at various scales, they’re as effective as at growing crops in skyscrapers as they are in 500 square foot studio apartments:
HYDROPONICS
One of the oldest and most common methods of vertical farming, hydroponics includes growing plants without soil and in a water solvent containing mineral nutrients. The simplest hydroponic method (called the floating raft system) suspends the plants in soilless raft like a polystyrene sheet and lets the roots hang to absorb the oxygen-aerated solution. Another common method is the nutrient film technique, which is popular for growing lettuce. Here, a stream of the nutrient-dissolved solution is pumped into an angled channel, typically a plastic pipe, containing the plants. This runs past the plants’ root mat and can then be recirculated for continuous use. New York’s Gotham Greens and Square Roots use hydroponics.
AEROPONICS
It’s no surprise that NASA has been backing research on aeroponic growth for the past two decades as it’s free-floating-roots aesthetic is typically used in futuristic sci-fi movies. With aeroponics, the dangling roots absorb a fine mist comprised of an atomized version of the nutrient solution sprayed directly onto the roots by a pump. Although aeroponics enables plants to grow much more quickly than hydroponics, it requires more solution and therefore is more costly. Newark’s Aerofarms uses aeroponics.
AQUAPONICS
Like hydroponic systems, an aquaponic system contains a soil-free plant bed suspended over a body of water containing nutrients necessary for plant growth. But within the body of water is a population of fish (typically herbivores) that produce waste that function as fertilizer for the plants. In turn, the plants help purify the water to make the water suitable for the fish.
Given that a balance must be achieved to ensure the system of both life forms, aquaponics requires greater attention than hydroponics or aeroponics although filtration and aeration systems can help manage these complications. Furthermore, the types of plants one can grow are much more limited as the necessary plant nutrients must be compatible with those necessary for the fish. Brooklyn’s Edenworks and Oko Farms use aquaponics.
By Matthew Sedacca | Edible Manhattan | May 3, 2017
Lead Illustration by Chamisa Kellogg